Mastering Mig Welding Tips


Introduction to Mig Welding
Mig welding, also known as Gas Metal Arc Welding (GMAW), is a popular welding process that uses a continuous wire feed as the electrode and an inert gas to protect the arc. This process is widely used in various industries, including automotive, construction, and manufacturing, due to its high speed, efficiency, and quality of welds. To master Mig welding, it is essential to understand the basic principles, equipment, and techniques involved.
Understanding Mig Welding Equipment
The Mig welding equipment consists of a welding machine, a wire feed system, a torch, and a shielding gas system. The welding machine provides the electrical power for the arc, while the wire feed system feeds the wire electrode at a consistent rate. The torch is used to direct the wire and shielding gas to the weld area, and the shielding gas system provides the inert gas to protect the arc.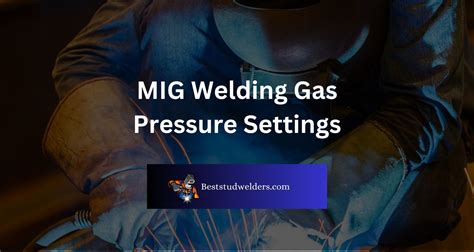
Setting Up for Mig Welding
To set up for Mig welding, follow these steps: * Ensure the welding machine is properly connected to the power source and the wire feed system is functioning correctly. * Select the correct wire diameter and type for the specific welding application. * Set the wire feed speed and voltage according to the manufacturer’s recommendations. * Connect the shielding gas system and set the flow rate according to the manufacturer’s recommendations. * Put on personal protective equipment, including a welding helmet, gloves, and safety glasses.
Mig Welding Techniques
To achieve high-quality welds, it is essential to master the following Mig welding techniques: * Push technique: This involves pushing the wire into the weld pool to achieve a smooth, consistent weld. * Pull technique: This involves pulling the wire out of the weld pool to achieve a more aggressive, penetrating weld. * Forehand technique: This involves holding the torch at a 10-20 degree angle, with the wire feeding out of the front of the torch. * Backhand technique: This involves holding the torch at a 10-20 degree angle, with the wire feeding out of the back of the torch.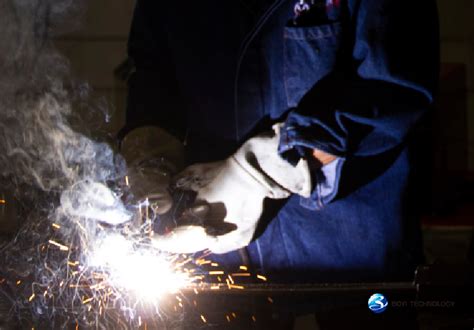
Tips for Improving Mig Welding Skills
Here are some tips for improving Mig welding skills: * Practice regularly to develop muscle memory and improve technique. * Use the correct equipment for the specific welding application. * Follow safety guidelines to prevent injury and damage to equipment. * Monitor the weld pool to ensure the correct temperature and penetration. * Adjust the wire feed speed and voltage as needed to achieve the desired weld quality.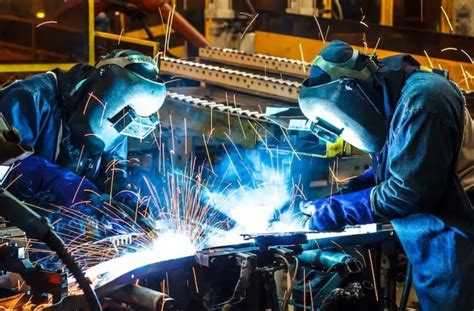
Wire Diameter | Shielding Gas | Wire Feed Speed | Voltage |
---|---|---|---|
0.8mm | 75% Argon, 25% CO2 | 2-4 m/min | 18-22V |
1.0mm | 80% Argon, 20% CO2 | 3-5 m/min | 20-25V |
1.2mm | 85% Argon, 15% CO2 | 4-6 m/min | 22-28V |
📝 Note: The wire diameter, shielding gas, wire feed speed, and voltage may vary depending on the specific welding application and equipment used.
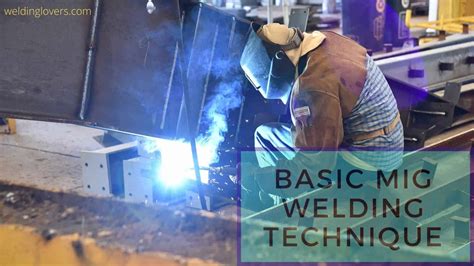
Maintenance and Troubleshooting
Regular maintenance and troubleshooting are essential to ensure the Mig welding equipment is functioning correctly. This includes: * Cleaning the wire feed system regularly to prevent clogs and misfeeds. * Checking the shielding gas system for leaks and damage. * Inspecting the torch for damage and wear. * Troubleshooting common issues, such as poor weld quality, wire feed problems, and shielding gas leaks.To summarize, mastering Mig welding requires a combination of understanding the equipment, techniques, and safety guidelines. By following the tips and guidelines outlined in this post, welders can improve their skills and achieve high-quality welds.

What is the difference between Mig and Tig welding?
+
Mig welding uses a continuous wire feed as the electrode, while Tig welding uses a non-consumable tungsten electrode. Mig welding is generally faster and more efficient, while Tig welding provides more precise control and better weld quality.
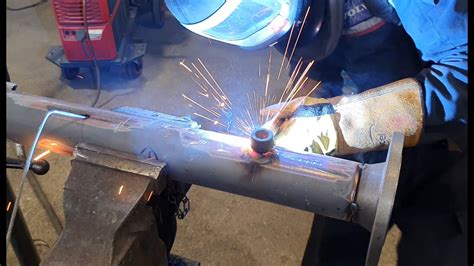
What is the best shielding gas for Mig welding?
+
The best shielding gas for Mig welding depends on the specific application and equipment used. Common shielding gases include Argon, CO2, and a mixture of the two.

How do I prevent porosity in Mig welds?
+
To prevent porosity in Mig welds, ensure the shielding gas is flowing correctly, the wire feed speed is consistent, and the weld pool is at the correct temperature. Additionally, use a high-quality wire and maintain a clean welding environment.